Solutions
- Valve part CAD / 3D pattern drawings are prepared which forms the foundation of a valve
- The valve functional testing is done first virtually on computer aided design software
- Then CAM data created for machining of Casting Patterns
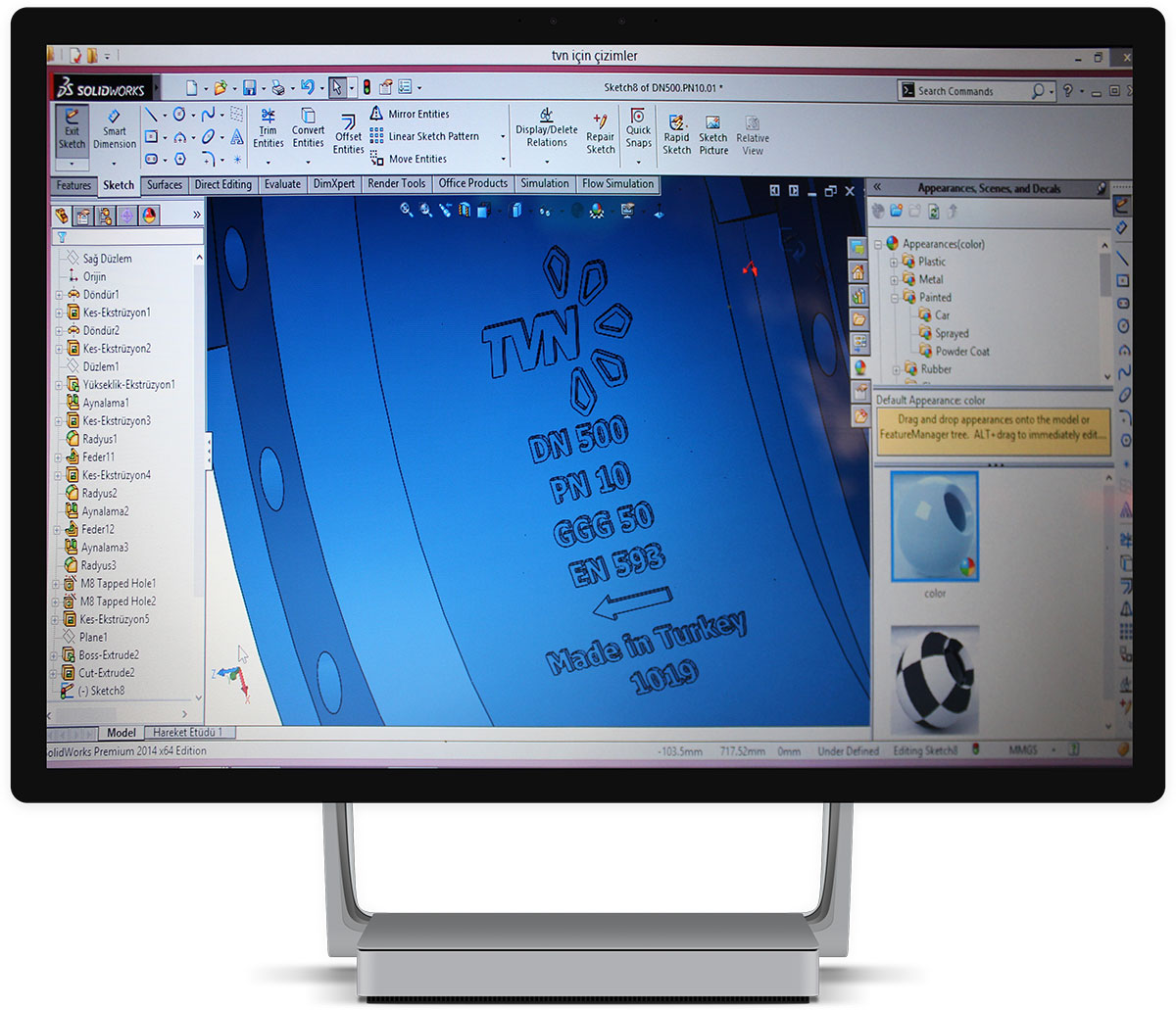
- Depending on casting volume, aluminium or wooden patterns are selected for specific valve types and sizes
- For automated moulding & casting lines, sets of aluminium patterns are prepared for faster casting speeds
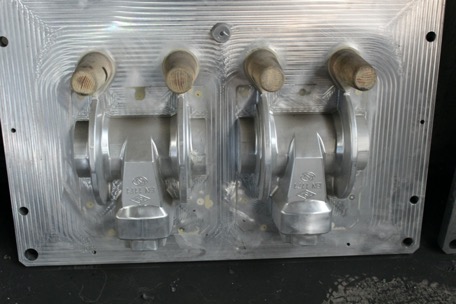
Aluminium GV Body Pattern
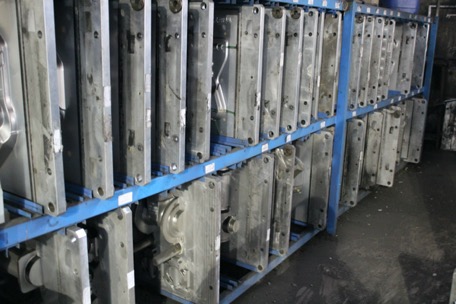
Aluminium Pattern Stock
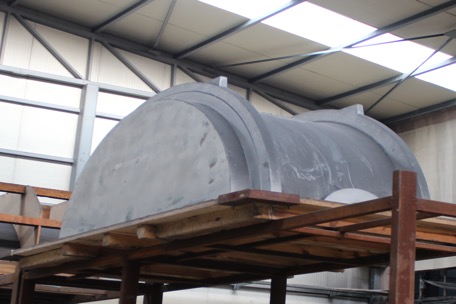
Wooden BFV Body Pattern
Foundry & Casting
- Full, semi automatic and manual moulding facilities
- Greensand / Resin Sand moulding Casting with core or without core Casting pieces from 0,1 to 8000 kg.
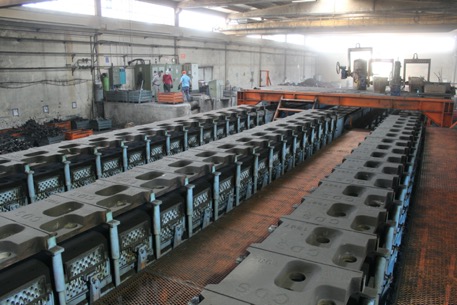
Full Automated Casting
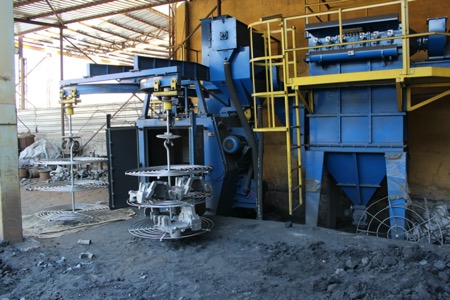
Sand/Shot Blasting After Casting
- High number of CNC machines
- Precise machining with CNC lathes
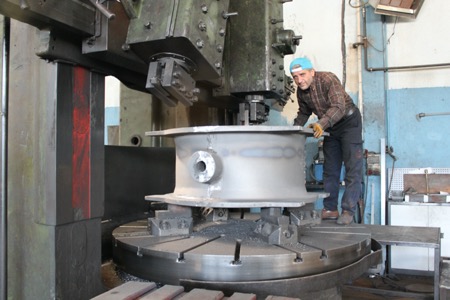
BFV Milling Machine
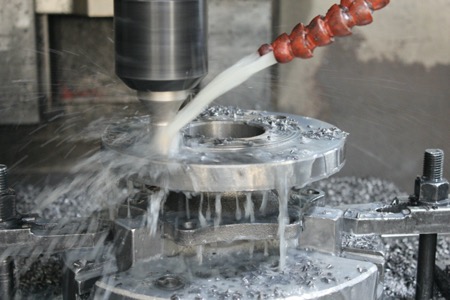
Ball Valve CNC Drilling
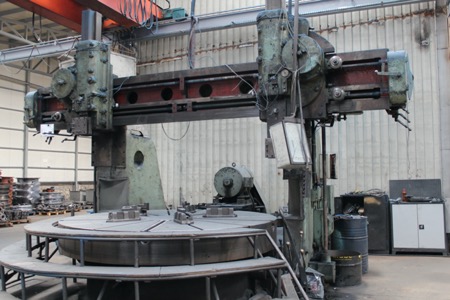
Machining up to DN3000

Turning Lathe
- Main type of coating is Electrostatic/Fusion Bonded Powder Epoxy
- All sizes, even biggest sizes are FBE coated
- Industrial/Spray Epoxy is also applied on certain type of valves
- Minimum 250-micron thickness for Powder Epoxy. Min. 300-micron or higher thicknesses are also available
- WRAS approved coating applied when specified
- Coating Inspection Report is created after process
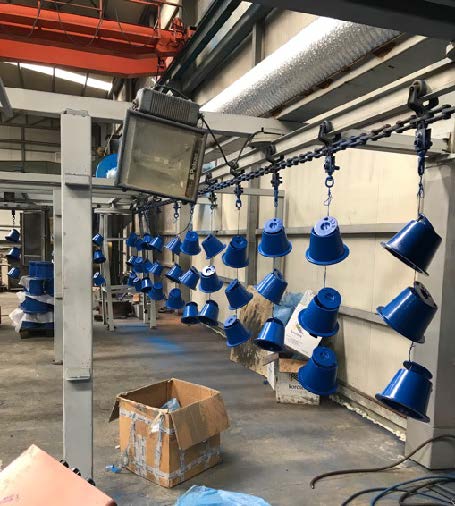
Automated Coating Line
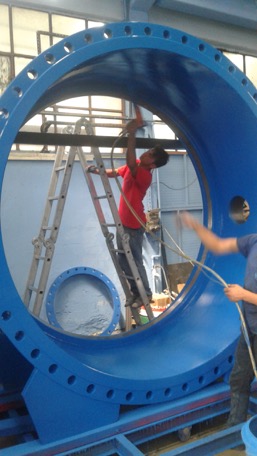
DN2200 During Coating
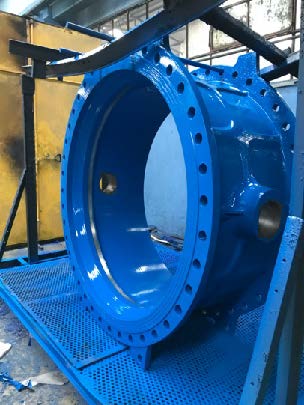
DN2200 After Coating
- Assembly staff is specialized on the assembly according to each product type
- Assembly guiding parts used for correct positioning
- Periodical assembly trainings are given to avoid missing parts and to increase efficiency
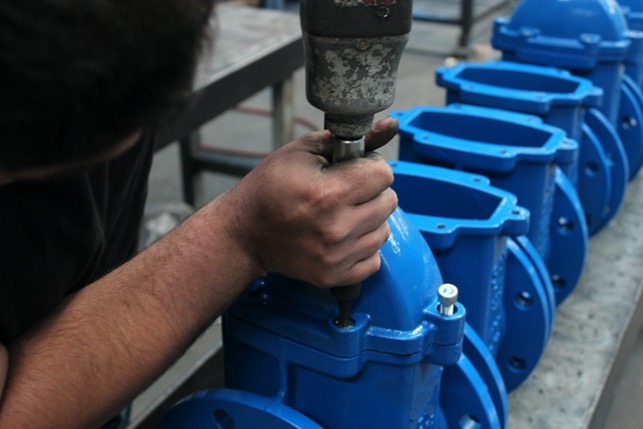
Gate Valve Assembly
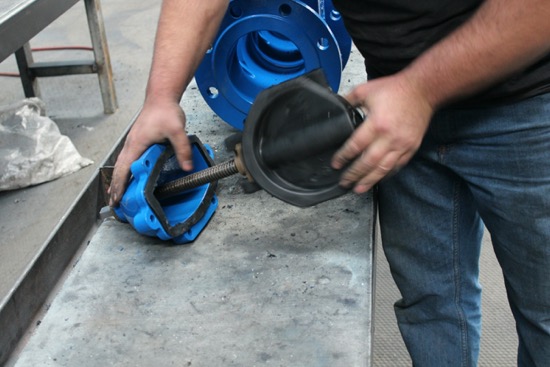
Gate Valve Assembly
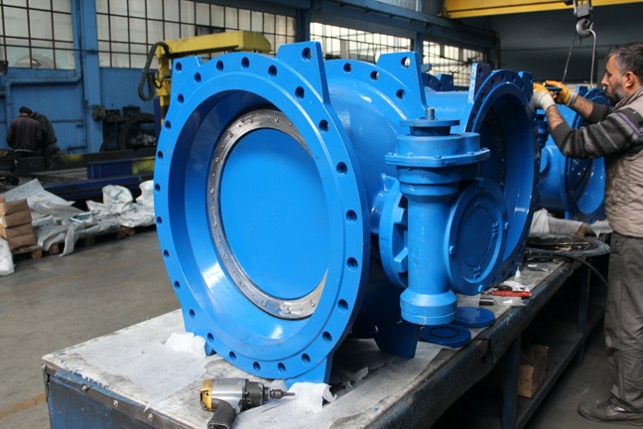
Butterfly Valve Assembly
- After assembly, each piece hydrostatically tested without exception according to EN12226-1 / EN12266-2 testing standards Rate A is our acceptance criteria
- Shell Test according to PN x 1.5
- Seat Test according to PN x 1.1
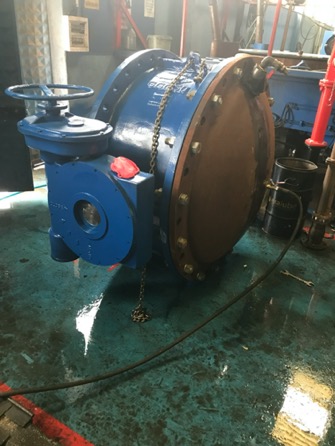
Seat Test with Blind Flange
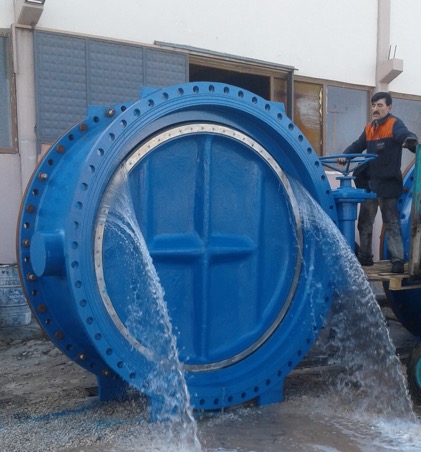
Big Size Outdoor Testing with Blind Flange
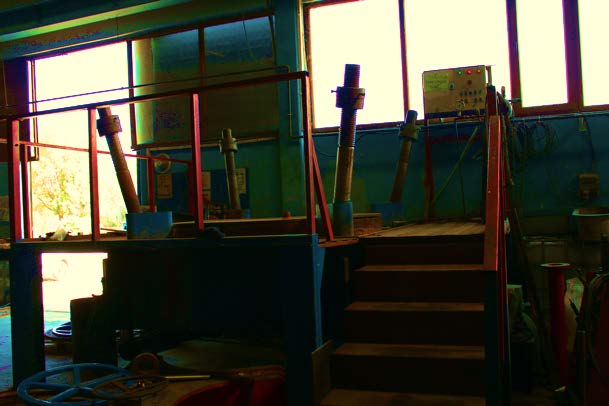
Test Bench up to DN1800